Solder Powder
Product
Electronic manufacturers require irreproachable solder powder geometry and metallurgical conditions to meet world-class quality standards for their applications. To that perspective, IPS has developed unique in-house atomization processes for conventional solder powders and for ultrafine solder powders. These processes are known to be the most efficient way for producing high quality and cost-competitive solder Powders. IPS invests a significant fraction of its revenues in R&D programs to keep its technological lead.
Size distribution
For other Particle Size Distribution, please contact us
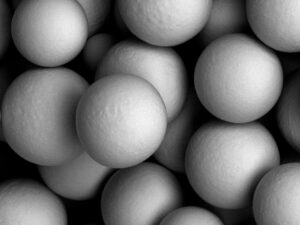
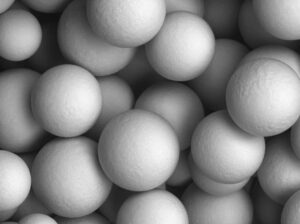
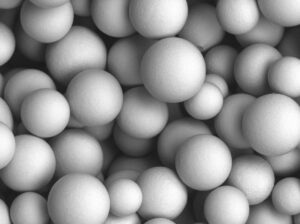
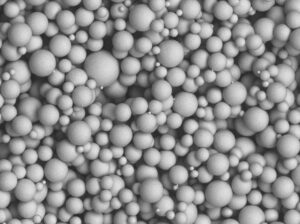
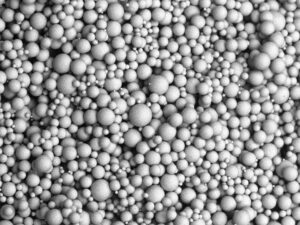
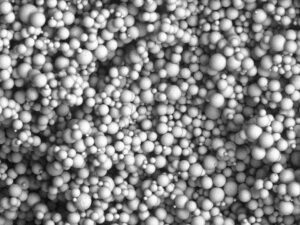
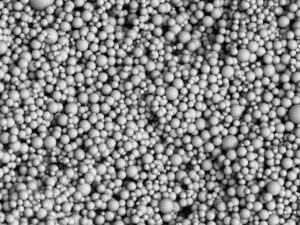
25-45μm
20-38μm
15-25μm
5-15μm
2-11μm
2-8μm
1-5μm
Alloy
IPS’ alloyed Solder Powders are produced using high purity metals. IPS’ range of Solder Powder offers a wide choice of alloy compositions with melting points up to 310°C ( 590°F ).
The flexibility of IPS manufacturing process allows the production of both industry standard and non standard Solder Powders in a broad range of alloys and characteristics to meet the needs of most manufacturers.
Alloy Characteristics | Sol °C | Liq °C |
---|---|---|
Sn42Bi58 | 138 | 138 |
Sn96Ag2.5Bi1Cu0.5 | 214 | 218 |
Sn95.5Ag4Cu0.5 | 217 | 219 |
Sn95.5Ag3.8Cu0.7 | 217 | 221 |
Sn98.5Ag1Cu0.5 | 221 | 221 |
Sn96.5Ag3.5 | 221 | 221 |
Sn96Ag4 | 221 | 229 |
Sn95Ag5 | 221 | 245 |
Sn96.5Ag3Cu0.5 (SAC 305) | 217 | 217 |
Sn99.3Cu0.7 | 227 | 227 |
Sn99Cu1 | 227 | 227 |
Sn97Cu3 | 227 | 300 |
Sn100 | 232 | 232 |
Sn95Sb05 | 232 | 240 |
Sn46Pb46Bi8 | 120 | 167 |
Sn43Pb43Bi14 | 144 | 163 |
Sn62Pb36Ag2 | 179 | 179 |
Sn62Pb35.6Ag2Sb0.4 | 179 | 179 |
Sn60Pb36Ag4 | 179 | 246 |
Sn63Pb037 | 183 | 183 |
Sn63Pb36.6Sb0.4 | 183 | 183 |
Sn60Pb40 | 183 | 191 |
Sn50Pb50 | 183 | 216 |
Sn10Pb88Ag2 | 268 | 290 |
Sn10Pb90 | 275 | 302 |
Sn05Pb92.5Ag2.5 | 287 | 296 |
Sn05Pb93.5Ag1.5 | 296 | 301 |
Sn05Pb95 | 308 | 212 |
Lead free alloys | Leaded alloys |
Applications
Solder powder is usually mixed with flux to form a solder paste. The choice of the particle size distribution and the nature of the alloy cover a wide range of needs: surface mounted technology, mini and micro-LED, semiconductor packaging, power electronic and battery assembly, etc. The excellent quality of our products allows them for military and aerospace application.
Mixed with the right corresponding flux, our solder powders and ultrafine solder powders are suitable for all uses: dispensing, jet printing (jetting), stencil printing, pin transfer.
The solder powder can also be used without flux for applications such as RFID antenna printing or other specific applications.
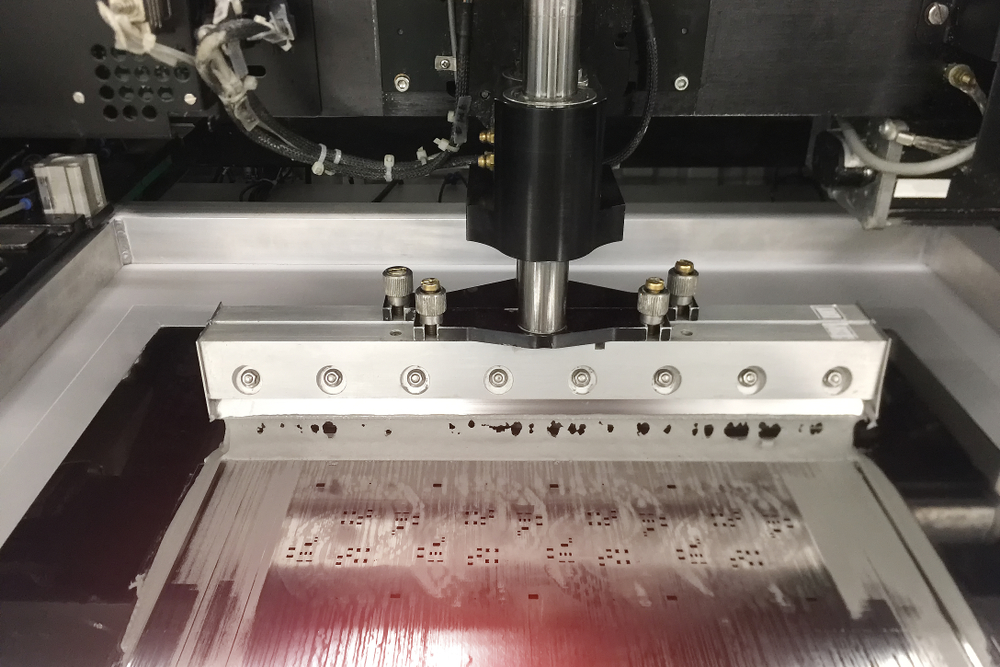
solder powders
solder powders
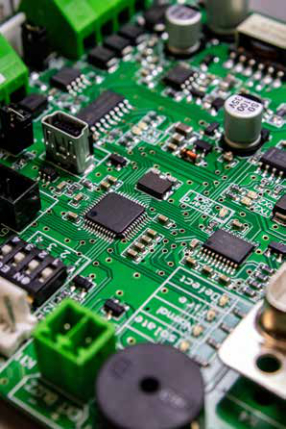
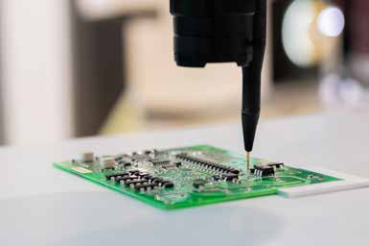
fine stencil opening
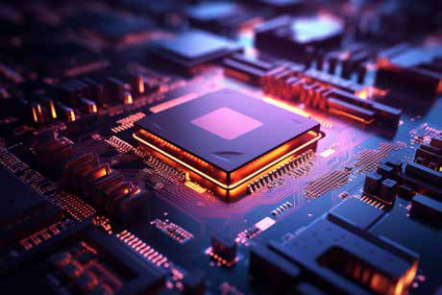
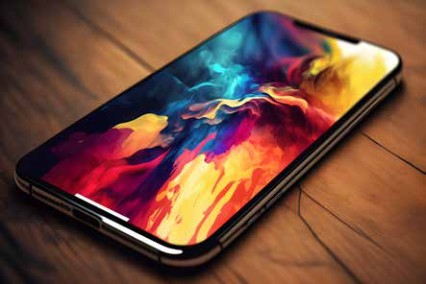
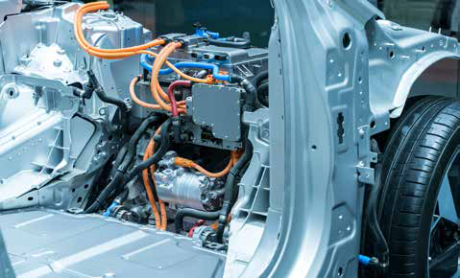
Battery assembly
solder powders
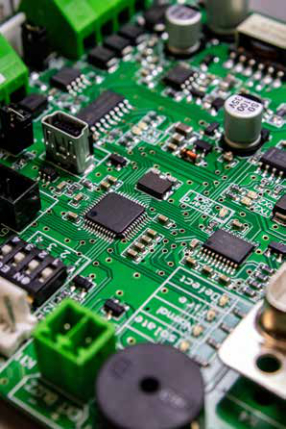
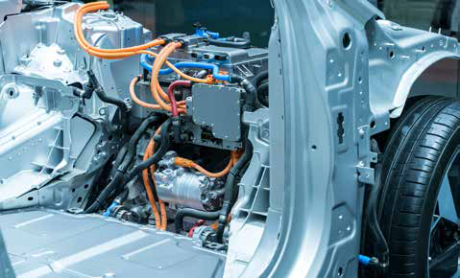
Battery assembly
solder powders
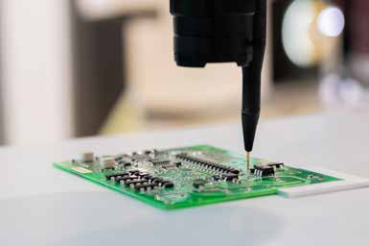
fine stencil opening
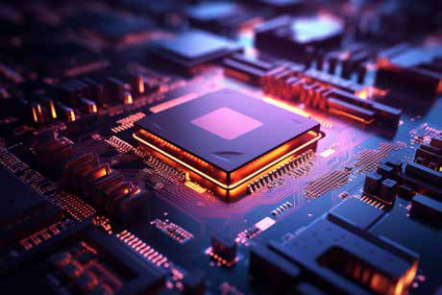
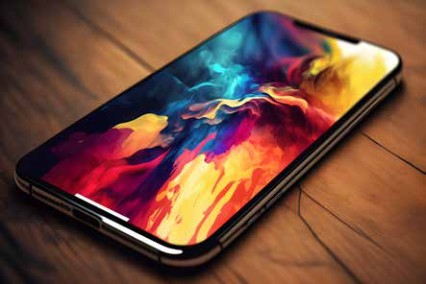
Quality control
IPS Solder Powders are manufactured through a severe Quality Management System that allows the company to serve the market with irreproachable products. Quality checks are performed at every stage of the production. As a standard procedure, properties tested on each manufacturing batch of Solder Powder include:
- Composition and impurity levels: The composition of each batch of alloy ingot and solder powder are analysed. Composition analysis is performed with spark spectrometer. All IPS Solder Powders meet or exceed J-STD-006 or ISO9453 international standards.
- Oxide content: Oxyde content is checked by chemical tests.
- Particle size distribution (PSD): PSD of the powder is double check using a laser diffraction particle size analyzer and an electronical image analysis system.
- Particle shape: Particle shape is checked by observation of the Solder Powder with a microscope at a set magnification in order to define the percentage of spherical or elliptical particles. IPS’ Solder Powders do have sphericity exceeding 95% (97% minimum for 20-38 micron standard Powder grade). All particles are free from surface defect.
- Solder balling: Note: that the solder balling performance of Solder Powder depends on the nature of the flux. For its standard QC procedure, IPS uses a mildly activated RMA rosin flux and / or no-clean flux. IPS can also perform solder balling test upon request using customer standard QC flux and test procedures.
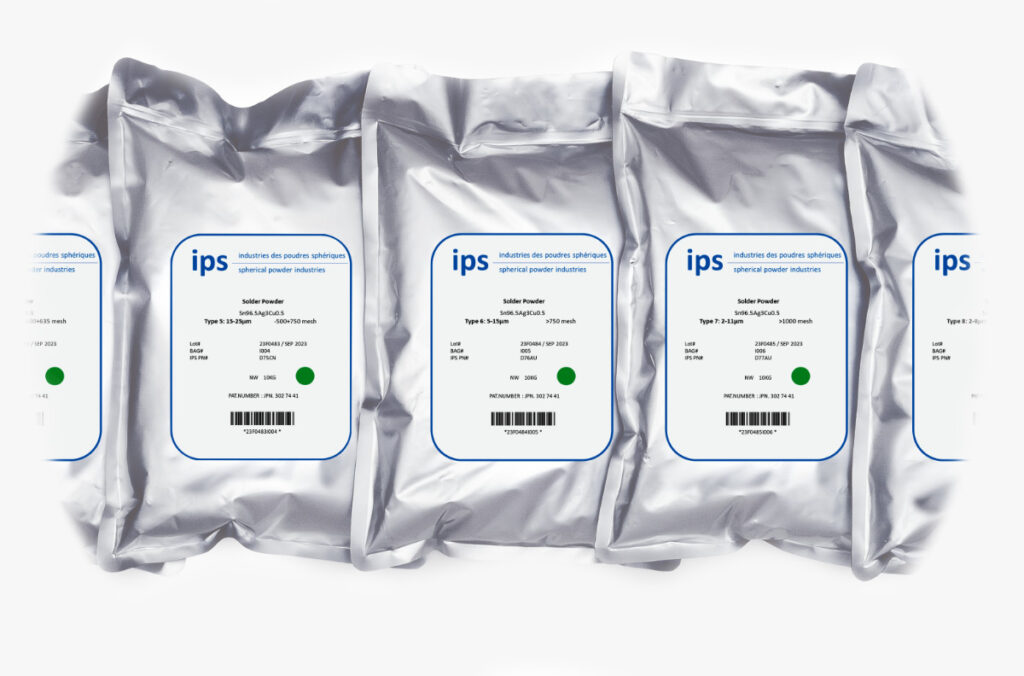
Packing
Each bag of solder powder is carefully inerted and packed to preserve all its properties during transport and storage. Robust aluminium bags selected after internal tests are used. Depending on customer requirements, the bags can be placed in plastic buckets and then packed in cartons or wooden boxes on pallets.